When it comes to running a business in Washington, understanding lock standards and safety regulations isn't just a matter of compliance; it's essential for protecting your assets and ensuring a safe environment for employees. The guidelines set by organizations like the Builders Home Manufacturers Association (BHMA) and the Washington Industrial Safety and Health Act (WISHA) are critical to follow. But are you aware of the specific requirements that could directly impact your operation? Consider how these regulations intertwine with workplace safety and what that means for your business's future.
Key Takeaways
- Washington businesses must comply with BHMA and ANSI lock standards, selecting appropriate grades for security needs based on their specific applications.
- Locksmiths in Washington must be licensed and insured to adhere to state laws governing lock picking and locksmithing practices.
- Regular inspections and maintenance of locks are essential for preventing lock failures and unauthorized access in compliance with safety regulations.
- Fire doors must meet specific compliance standards, including proper labeling and functionality, to ensure safety during emergencies and fire containment.
- Panic hardware must be installed following regulations, allowing easy egress during emergencies, with specific height and force requirements for operation.
Importance of Lock Standards
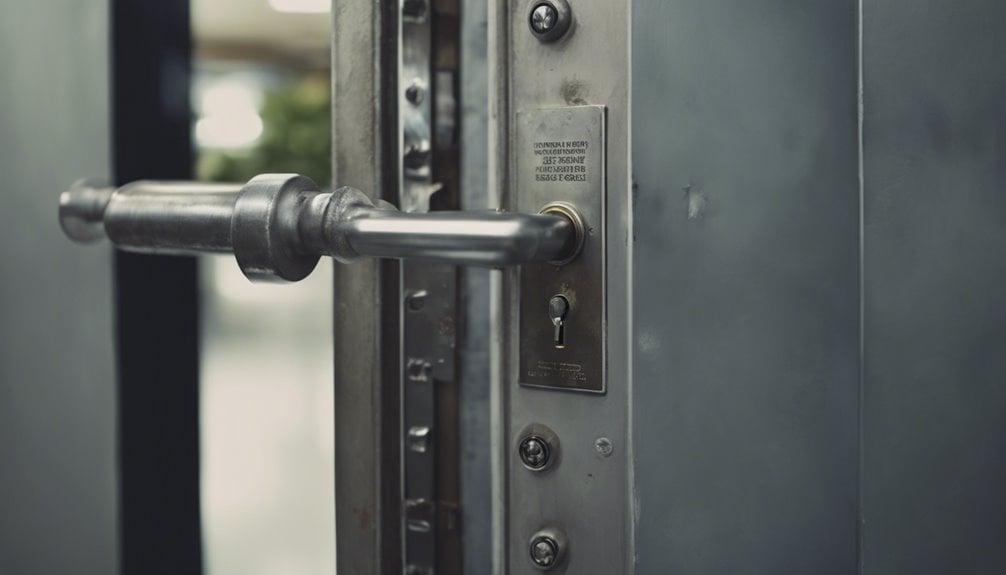
Lock standards are fundamental for guaranteeing the security and functionality of commercial spaces. The Builders Home Manufacturers Association (BHMA), accredited by the American National Standards Institute (ANSI), sets these key standards, grading locks based on important attributes such as application, durability, and security.
Adhering to these standards isn't just a matter of compliance—it's about selecting the right lock grade that aligns with your business's specific security needs. When you choose locks that meet the required grades, you confirm that they possess the quality and specifications necessary to protect your commercial space effectively. In Washington, high-security lock regulations ensure that locks installed in homes meet stringent criteria to enhance security. Landlords and tenants in Washington should also understand the legal guidelines for changing locks in rental properties to ensure compliance with state regulations.
This choice dramatically impacts your security levels, preventing unauthorized access and minimizing risks associated with lock failures. Regular maintenance of these locks is essential, as wear and environmental factors can lead to malfunctions that jeopardize both security and accessibility. In fact, regular inspections can identify early signs of wear and prevent keys from breaking in locks, thereby reducing major security threats.
Moreover, compliance with lock standards is non-negotiable for maintaining operational integrity. Locks must meet specific industry regulations, including those set forth by the ADA, guaranteeing accessibility for everyone.
This attention to detail not only helps you avoid penalties and legal consequences but also reflects your commitment to an inclusive environment. In a world where security is paramount, understanding and implementing these lock standards empowers you to make informed decisions.
Overview of Safety Regulations
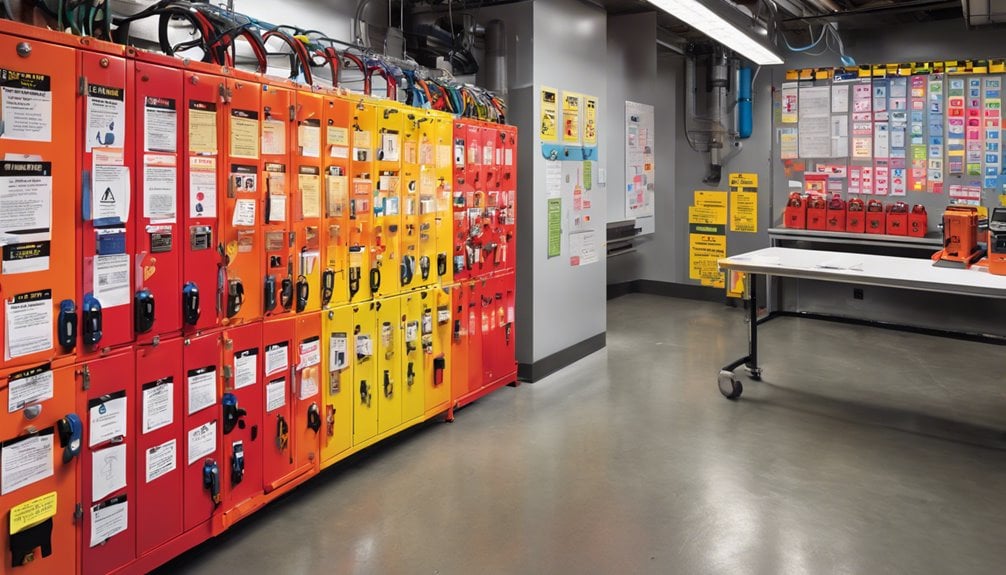
While ensuring the safety of your workplace, it's crucial to understand the safety regulations set forth by the Washington Industrial Safety and Health Act (WISHA). Enforced by the Division of Occupational Safety and Health (DOSH), WISHA applies to most employers in Washington, mandating compliance through inspections and training.
While DOSH provides important resources, you're responsible for implementing safety measures in your organization. In Washington State, understanding lock picking laws is also essential for businesses that deal with locksmithing or use of lock picking tools, ensuring they remain compliant with local regulations. Furthermore, businesses should ensure their locksmiths are licensed and insured to adhere to state requirements and enhance trustworthiness.
To maintain a safe environment, you must provide substantial safety training to your employees. This training should cover hazard identification, the proper use of personal protective equipment (PPE), emergency response procedures, and first-aid training, ensuring everyone knows how to react during an emergency. WISHA emphasizes ergonomics training is also necessary for promoting workplace safety.
Identifying and controlling workplace hazards is another critical aspect of WISHA regulations. You must address risks such as bloodborne pathogens, fire safety, and electrical issues. Adhering to the Lockout/Tagout (LOTO) Standard is crucial when performing maintenance to control hazardous energy sources.
Additionally, you need to inform employees about hazardous materials present in your workplace.
Promptly reporting workplace injuries isn't just a requirement; it helps expedite necessary corrective actions and compliance. Regular safety meetings and adherence to WISHA's compliance checklist will help you maintain a safe, responsive workplace.
Failing to comply with these regulations could lead to fines and penalties, hindering your business's success. Understanding and implementing WISHA's safety regulations affords you the freedom to operate securely and efficiently.
ADA Compliance for Accessibility
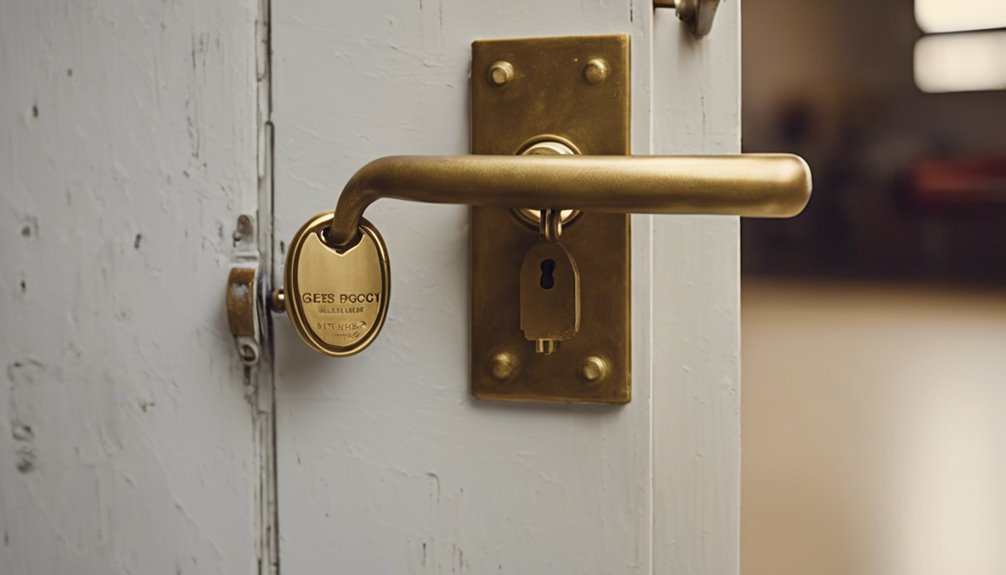
When considering ADA compliance, pay close attention to door hardware specifications and clearance space requirements. Doors must have appropriate handles that are easy to operate, as well as sufficient clearances to accommodate wheelchair access without obstruction. Verify that all paths leading to and around doors meet the required space dimensions to facilitate smooth navigation for individuals with disabilities. In Washington State, locksmiths play a vital role during eviction procedures, ensuring proper access control and security are maintained. Additionally, ensuring compliance with Policy 188 enhances usability for all individuals, including those using assistive tech. It is essential for locksmiths in Washington to understand rekeying laws to ensure their services align with state regulations.
Door Hardware Specifications
To guarantee your business meets ADA compliance, it's essential to properly specify door hardware that facilitates accessibility for all users. Consider these key guidelines:
1. Height and Placement: Place operable parts of door hardware between 34 and 48 inches above the finished floor. Confirm consistency and avoid any projections below 34 inches.
Door closers should be at least 78 inches high.
2. Operability Requirements: Select hardware that's operable with one hand, requiring no tight grasping, pinching, or wrist twisting. Favor lever-operated or push-type mechanisms; these allow use with a closed fist or loose grip, limiting activation force to a maximum of 5 pounds.
3. Types of Compliant Hardware: Choose lever handles instead of knobs to comply with ADA standards. Verify locks, exit devices, and panic bars meet the necessary operability criteria. Operating as an unlicensed locksmith in Washington carries significant risks and potential penalties, making it crucial to ensure all business practices comply with local laws.
Regular maintenance and prompt repairs are essential to keep your door hardware functional and compliant. Additionally, understanding business regulations and marketing strategies is important for locksmiths to navigate industry challenges effectively.
Clearance and Space Requirements
Guaranteeing compliance with ADA regulations requires careful attention to clearance and space requirements within your business. You must provide at least one accessible route from public transportation stops and parking spaces to your building's entrance. These routes must meet specific technical specifications, including clear widths and slopes, guaranteeing they remain continuous and unobstructed.
For public and common areas, remember to create accessible pedestrian spaces. Clearances for parking, seating, and desks must be obstacle-free and wide enough to accommodate easy movement. Check that access aisles for van-accessible parking spaces measure at least 60 inches wide and 20 feet long. Locksmiths in Washington must adhere to these ADA requirements to ensure that their services and facilities are accessible to all customers.
If your business involves dwelling units, guarantee that these spaces allow for adequate maneuverability in kitchens and bathrooms. You should strategically place light switches and outlets within reach and reinforce areas for the future installation of grab bars around fixtures.
For existing buildings, focus on removing architectural barriers that are easily achievable without significant expense. Consider using the 1991 or 2010 ADA Standards when making alterations. When dealing with digital locks and smart security systems, ensure that their installations comply with the legal considerations specific to Washington, ensuring that these systems do not impede accessibility.
Fire Safety Requirements
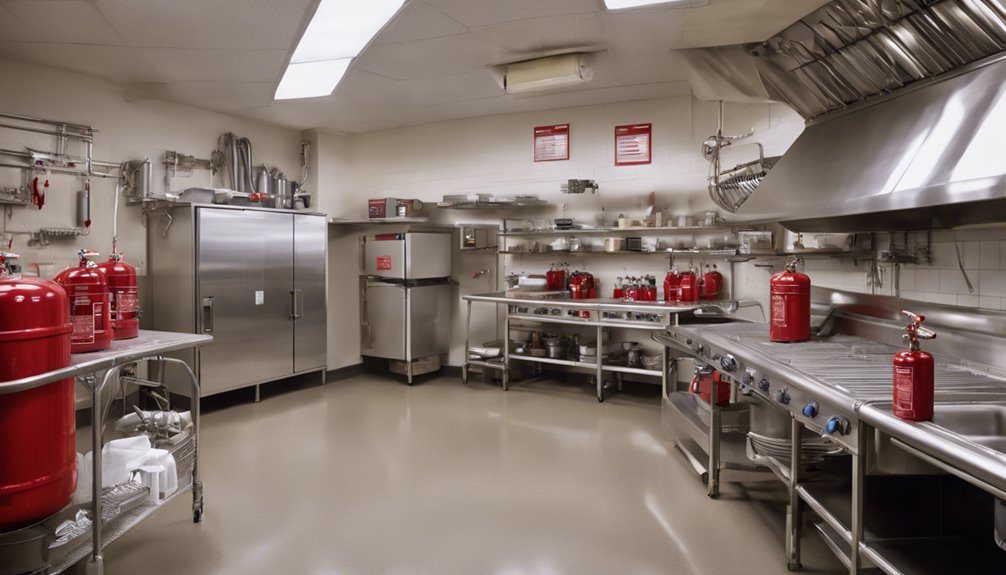
When managing fire safety in your workplace, it's essential to comply with fire door standards to guarantee effective containment during a fire event. Regular inspections of these fire doors are necessary to verify they function properly and meet safety regulations. Stay vigilant in your upkeep to protect both your employees and property from potential fire hazards. For businesses in need of emergency locksmith services, having access to a 24-hour mobile locksmith(#) can be a critical component of your overall safety plan.
Fire Door Compliance Standards
Fire door compliance standards are critical for maintaining safety in commercial buildings, as they not only serve as barriers against smoke and flames but also guarantee safe egress during emergencies.
To verify your fire doors meet the necessary regulations, you'll need to adhere to the following key standards:
- Labeling: Fire doors must have a visible and legible label showing their fire resistance rating, typically located on the hinge edge.
- Hardware Requirements: Utilize only fire-rated hinges, such as ball bearing types, and verify all hardware is tested and marked for fire door use. Smoke seals are necessary if the door has an "S" indicator.
- Egress Compliance: Make sure that fire doors allow free exit without mechanical locking or latching. The maximum force required to open the door shouldn't exceed prescribed limits, verifying swift escape when needed.
Regular Inspection Necessity
Regular inspections play an essential role in maintaining fire safety within your business premises, as they help identify potential hazards and guarantee compliance with established regulations. Adhering to inspection schedules is vital; for example, high hazard occupancies need annual inspections, while moderate hazards require them biennially. In numerous jurisdictions, including the District of Columbia, these inspections are significant for business license renewal.
Here's a quick reference table to understand different inspection requirements:
Occupancy Type | Frequency | Notes |
---|---|---|
High Hazard | Annual | Needs thorough annual assessment. |
Moderate Hazard | Biennial | Compliance checks for regulations. |
Childcare Facilities | Every 3 years | Inspected upon request from DCYF. |
Fire Alarm Systems | Annual Service | Must be verified post-inspection. |
Egress Routes | Ongoing Maintenance | Must be clear and unobstructed. |
Locks and Latches Codes
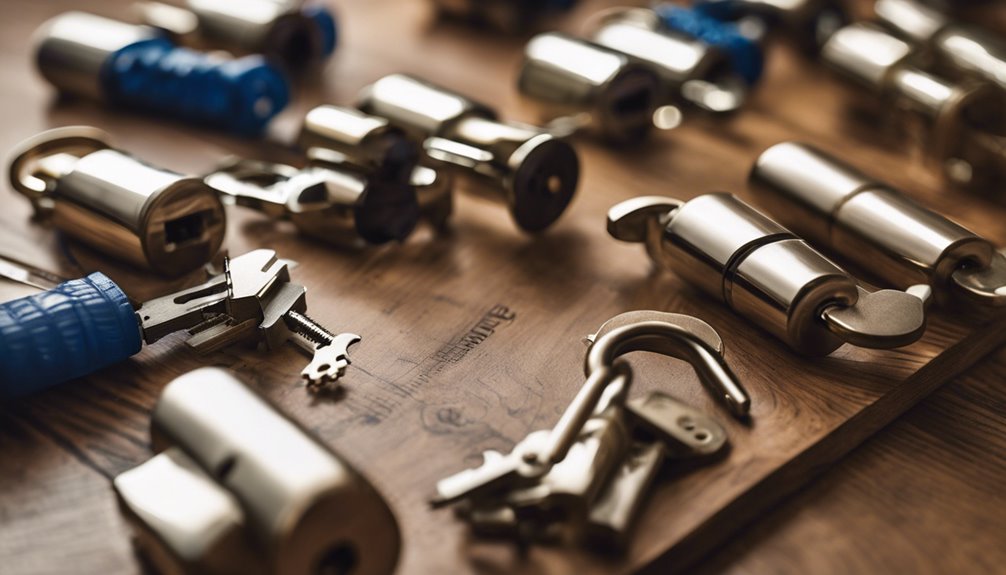
Guaranteeing compliance with locks and latches codes is essential for maintaining safety and accessibility in Washington businesses.
These codes not only enhance security but also guarantee that everyone can access buildings without unnecessary barriers. Knowing the regulations can help you avoid penalties and contribute to a safer environment.
Here are three key points to take into account:
- ADA Compliance: Locks and latches must be operable with one hand, requiring no tight grasping, pinching, or wrist twisting. The maximum force for operation shouldn't exceed 5 pounds to guarantee accessibility for all individuals.
- Fire Safety Standards: If you have fire-rated doors, they need to comply with IBC and NFPA standards. Locking devices are only permitted if they don't impede safe evacuation when temperatures rise. Proper labeling according to fire door test procedures is also mandatory.
- Occupancy-Specific Regulations: Certain occupancies have unique requirements. For instance, key-operated locks on main doors may require specific signage to enhance visibility, and particular egress doors may need additional safety systems such as automatic sprinklers or smoke detection.
Panic Hardware Specifications
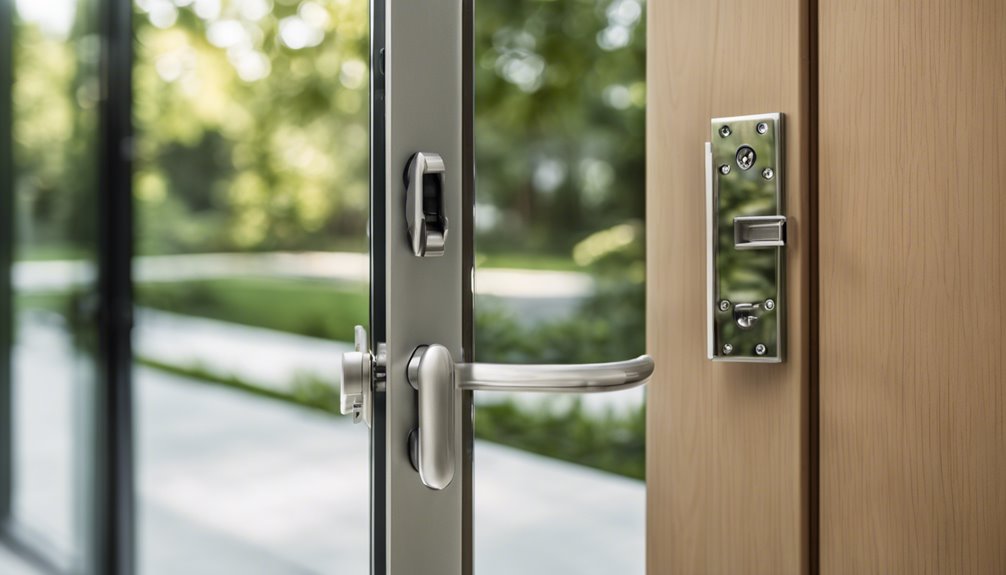
When it comes to panic hardware, you need to verify compliance with specific standards and regulations outlined for your facility.
This includes adhering to installation requirements, verifying the hardware meets code compliance for your occupancy type, and conducting regular inspection protocols to maintain functionality.
Familiarizing yourself with these standards will help guarantee a safe exit path during emergencies.
Required Panic Hardware Standards
To comply with safety regulations, you must understand the specific panic hardware standards outlined by the International Building Code (IBC) and the National Fire Protection Association (NFPA) for various occupancy types.
These standards guarantee safe egress in emergencies and are vital for your business.
Here are the essential panic hardware standards to follow:
- Installation Height: Panic hardware must be mounted between 34 inches and 48 inches above the floor.
- Force Requirements: The hardware must operate with a maximum of 15 pounds of force, or 5 pounds for certain codes, assuring easy access.
- Occupancy Criteria: Panic hardware is required for assembly, educational, high hazard, and daycare occupancies, depending on the occupant load as defined by the IBC and NFPA.
Compliance and Inspection Protocols
Understanding compliance and inspection protocols for panic hardware is vital for maintaining safety standards within your business. Following the Washington Industrial Safety and Health Act (WISHA) and federal OSHA regulations is significant. Regular inspections from DOSH guarantee your workplace meets these mandates, covering exit routes, signage, and emergency procedures.
Here's a quick reference table summarizing key compliance aspects:
Compliance Aspect | WISHA Requirements | OSHA Requirements |
---|---|---|
Exit Routes and Doors | Must be operable and maintained | Must lead directly outside and be properly labeled |
Signage | Specific design and language mandated | "This door to remain open" signs must be posted |
Emergency Procedures | Defined procedures for alarm sounds and exits | Regular testing and clear exit signs required |
Inspector Duties | Check compliance with safety standards | Enforce additional codes (UFC, NEC) |
Maintaining compliance with local fire, building, and electrical codes is equally important. Remember, regular updates and inspections will help you uphold safety standards and protect your employees' freedom in emergency situations. Stay proactive about these regulations, guaranteeing your business remains a safe place to work.
Wind Load Considerations
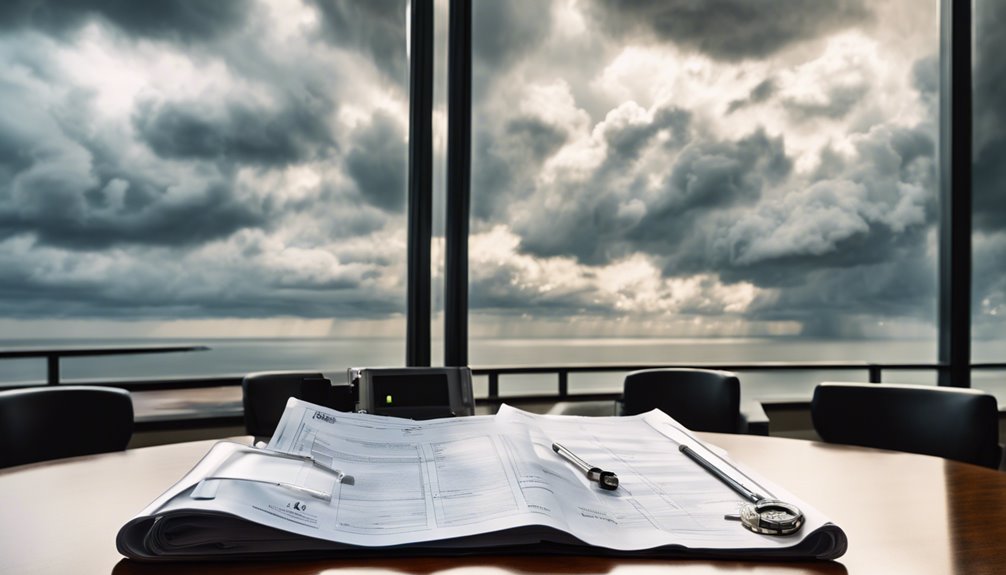
As you plan your construction project in Washington, it's essential to take into account wind load factors that directly impact structural safety and compliance. Understanding these factors not only helps guarantee the safety and durability of your structure but also adheres to local regulations.
Here are three key considerations for wind load:
- Risk Categories and Wind Speeds: Each structure falls under a specific Risk Category, which determines the required wind speed for compliance. For instance, a Risk Category II structure mandates a 3-second gust wind speed of 97 mph, while a Category IV structure necessitates 107 mph.
- Exposure Categories: Your project's location determines its exposure category, which can impact wind load requirements. Structures within 1,500 feet of the Columbia River will classify under Exposure Category C, while those near shorelines may require Category D due to their vulnerability to higher wind loads.
- Local Regulations: Always check local amendments and regulations, as cities like Seattle have specific standards that may differ from state guidelines. Local maps provide clarity on exposure categories and wind load factors, guaranteeing you adhere to pertinent regulations.
Energy Efficiency in Doors
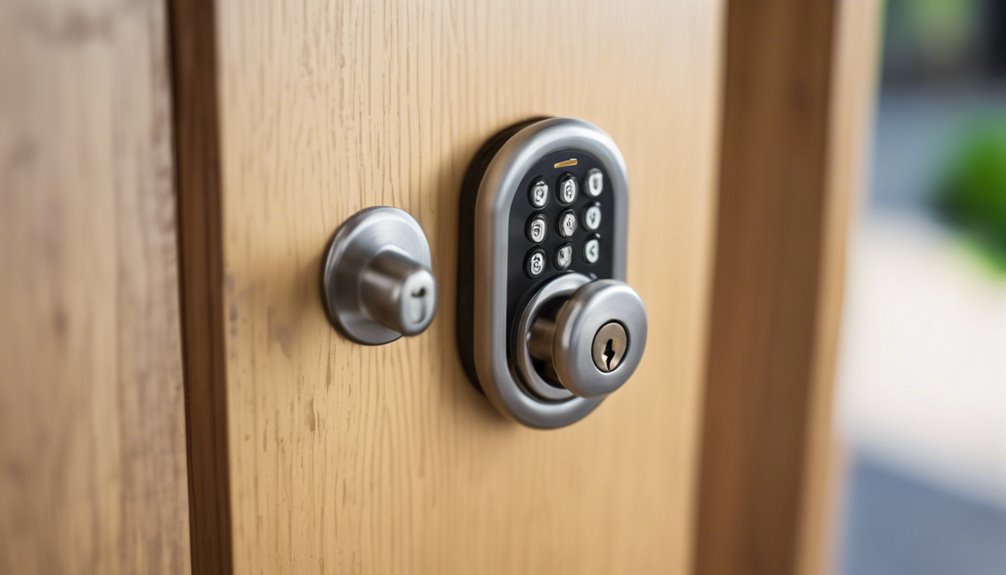
Wind load considerations highlighted the importance of structural integrity, but energy efficiency in doors plays an essential role in enhancing the overall performance of your building. Selecting the right materials can greatly impact your energy costs and comfort.
Solid-core wood doors, for instance, offer exceptional insulation due to their density, while commercial metal doors made from steel or aluminum can be energy-efficient when equipped with thermal breaks or insulated cores. Fiberglass doors excel in energy efficiency thanks to their poor heat conduction properties and enhanced insulation.
Ensuring your doors are well-insulated is imperative; materials like polyurethane or polystyrene maximize thermal resistance, while high-quality door seals and weatherstripping—using silicone or neoprene—prevent air leaks.
Consider using automatic door bottoms that close tightly for improved energy performance. Incorporating insulated cores into your doors will considerably reduce temperature fluctuations.
Automated door solutions can also enhance energy efficiency. These systems open and close only when necessary, decreasing unwanted air exchange.
Programmable door systems optimize their operation, while occupancy sensors adjust their timing based on environmental conditions, especially in high-traffic areas.
Moreover, balancing energy efficiency with security is essential. High-security doors made from steel can be designed with insulation and thermal breaks without sacrificing safety.
Workplace Safety Regulations
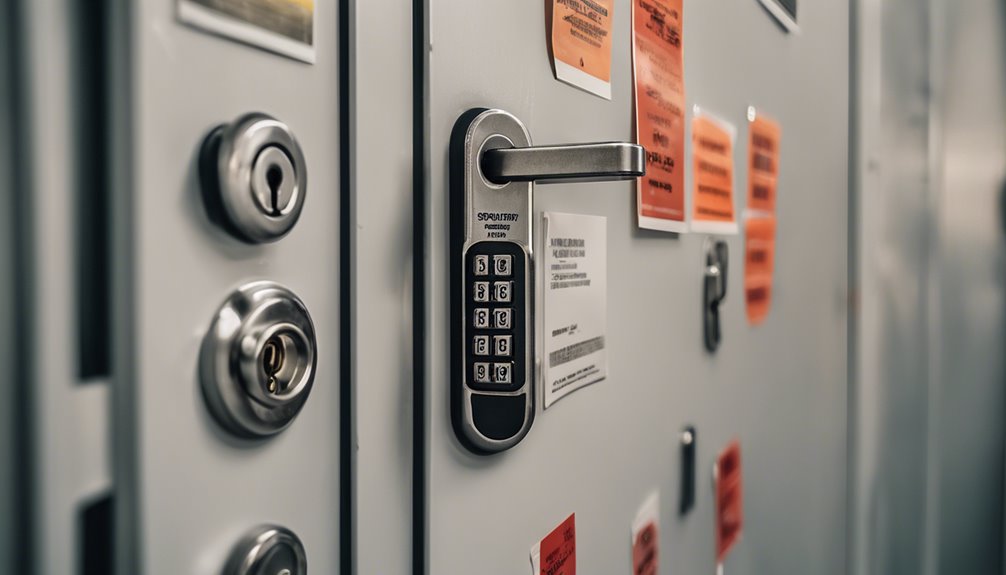
Creating a safe and healthy work environment isn't just a regulatory obligation but an essential aspect of maintaining employee well-being and productivity.
As a business owner in Washington, you must comply with workplace safety regulations designed to protect your workforce. This involves implementing specific programs and ensuring consistent training and involvement.
To help you navigate these responsibilities, consider focusing on the following key areas:
- Safety Programs: Develop and maintain a written safety and health program that addresses specific workplace hazards. Make sure to post the Job Safety and Health Law poster to inform employees about their rights and responsibilities.
- Training and Involvement: Provide thorough training on job safety, emphasizing hazard recognition and emergency procedures. Involve your employees in safety decision-making processes, fostering accountability within your safety program.
- Hazard Abatement: Implement an Accident Prevention Program (APP) to systematically identify and mitigate potential hazards.
Regular inspections and compliance with hazard communication standards, such as labeling hazardous substances, are vital steps in maintaining a safe environment.
Regular Compliance Inspections
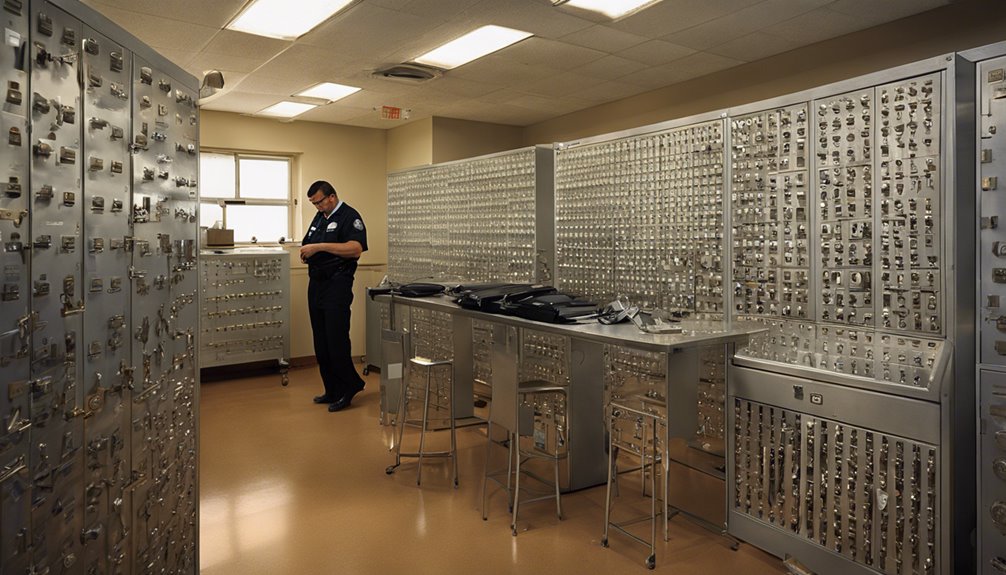
Regular compliance inspections are vital for guaranteeing that your business meets safety standards and regulations, especially regarding fire alarm systems. In Washington State, these inspections must occur annually to comply with the National Fire Alarm and Signaling Code (NFPA Standard 72) and local regulations. They serve to confirm your systems are functioning correctly and able to respond in emergencies.
During inspections, trained professionals will evaluate all fire alarm devices, checking for impairments and confirming maintenance is performed as needed. This rigorous process not only maintains compliance with the authority having jurisdiction (AHJ) but also protects your business and employees by preserving the integrity of fire and life safety devices.
Utilizing advanced inspection technology, such as BuildingReports, can enhance this process. The point-and-scan tool minimizes human error and accelerates inspections while eliminating outdated paperwork. With data stored securely online, you and other stakeholders, like insurance companies and local authorities, can easily access detailed reports that document all findings and necessary repairs.
Maintaining accurate inspection records is vital for demonstrating compliance. These reports provide a clear account of your adherence to regulatory standards and serve as essential documentation if you ever face scrutiny.
Regular compliance inspections guarantee your fire safety systems operate effectively, shielding your business from potential hazards and ensuring you're covered by insurance. Don't compromise on safety—stay compliant and maintain peace of mind.
Frequently Asked Questions
How Often Should Locks Be Replaced for Security?
You should replace locks every five years to maintain maximum security.
Regular replacements guarantee that wear and tear don't compromise your safety.
However, immediate replacement is necessary after any security breach, employee turnover, or lost keys.
If you notice a lock that's difficult to use, replace it promptly.
Establishing a proactive strategy for lock maintenance strengthens your security and protects your business from unauthorized access or potential breaches.
What Types of Locks Are Best for High-Traffic Areas?
In this modern age, ensuring security in high-traffic areas demands selecting the right lock types.
You'll want to evaluate commercial-grade locks for their durability and security features. Keyless entry locks offer convenience and the elimination of key duplication.
Electric strikes provide effective one-sided security, while heavy-duty locks resist wear and tear from constant use.
Choose wisely to enhance both accessibility and safety in your environment, ensuring a seamless flow of freedom and protection.
Are There Specific Locks for Outdoor Vs Indoor Use?
Yes, there're specific locks designed for outdoor and indoor use.
Outdoor locks need to be weatherproof and secure against tampering, often equipped with features like automatic opening in emergencies.
Indoor locks can include deadbolts or latches that guarantee privacy while allowing quick exits.
It's crucial to select locks that meet safety regulations while maintaining accessibility for residents and staff, guaranteeing both security and freedom of movement in shared spaces.
How Can I Improve My Door Security Beyond Locks?
Imagine your door as a steadfast knight protecting your castle.
To bolster that defense, opt for solid materials like metal or thick wood. Reinforce it further with heavy-duty deadbolts and strike plates that resist intrusion.
Consider installing a security system with alarms and motion detectors, turning your door into a vigilant guardian.
Access control measures, like keycards, enhance security while granting you freedom to manage who enters your space.
Your sanctuary deserves such fortified protection.
What Should I Do if My Lock Malfunctions Unexpectedly?
If your lock malfunctions unexpectedly, first identify the type and cause of the issue—it might be mechanical or linked to power loss.
Notify your building officials right away and fill out a hazard alert form. Use barricades or signage to guarantee safety until repairs are made.
Engage a certified locksmith for a permanent fix and maintain documentation of the incident.
Regular maintenance checks are essential to prevent future problems and keep your space secure.
Conclusion
In summary, adhering to lock standards and safety regulations isn't just a necessity; it's your business's shield against potential hazards. Think of compliance as the sturdy lock on your door—it secures your workplace, keeps employees safe, and protects your investments. By staying informed and vigilant, you guarantee that your foundation is solid, paving the way for a secure and efficient operation. Embrace these regulations, and you'll build a fortress of safety that fosters trust and success.